Why This Topic Matters Now
Choosing the right type of marine fender can save ports and shipowners from costly damages and delays. For example, one of our clients operating a floating LNG terminal faced repeated downtime using the wrong type of fender—until switching from foam to pneumatic fenders drastically improved performance. That’s why understanding the differences and application scenarios of foam fenders and pneumatic fenders is not just important—it’s essential.
What Are Pneumatic Fenders?
Pneumatic fenders, often known as Yokohama fenders, are constructed with reinforced rubber layers and filled with compressed air. They are flexible, lightweight, and absorb energy by compressing air during ship-to-ship or ship-to-dock operations. These fenders are commonly seen with protective chains, tires, or web-nets on their surface.
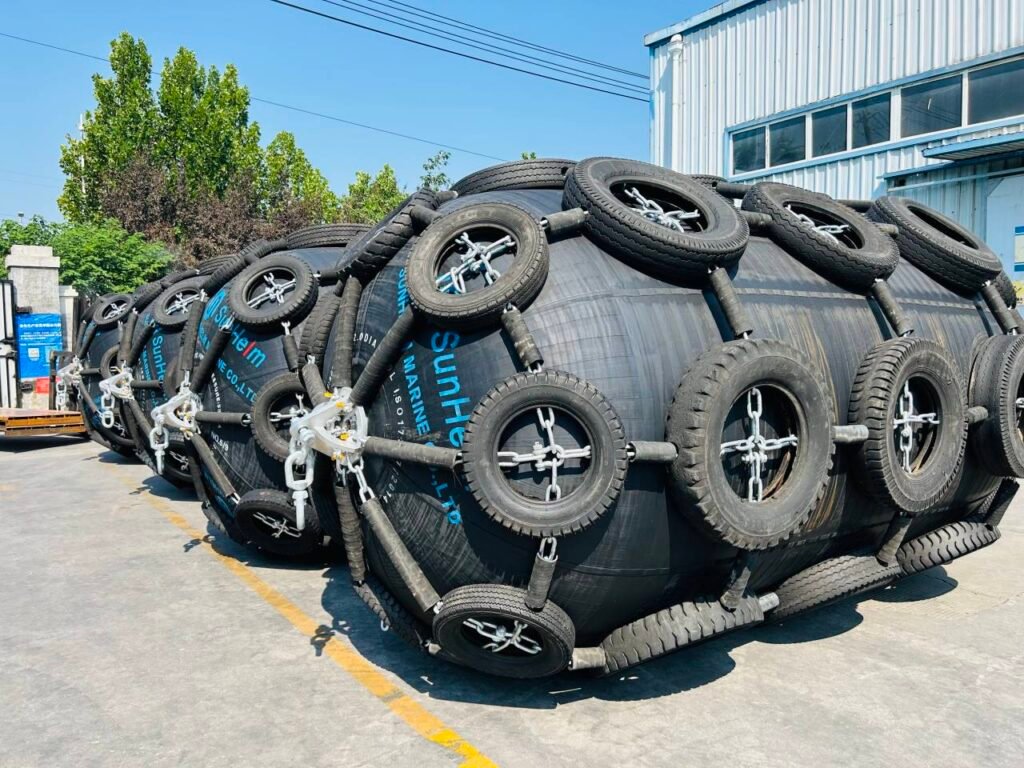
What Are Foam Fenders?
Foam-filled fenders use a closed-cell foam core that is highly durable and unsinkable. They have an outer polyurethane or rubber skin and can withstand direct impact without losing shape. Even when punctured, foam fenders maintain their performance since there’s no air involved.
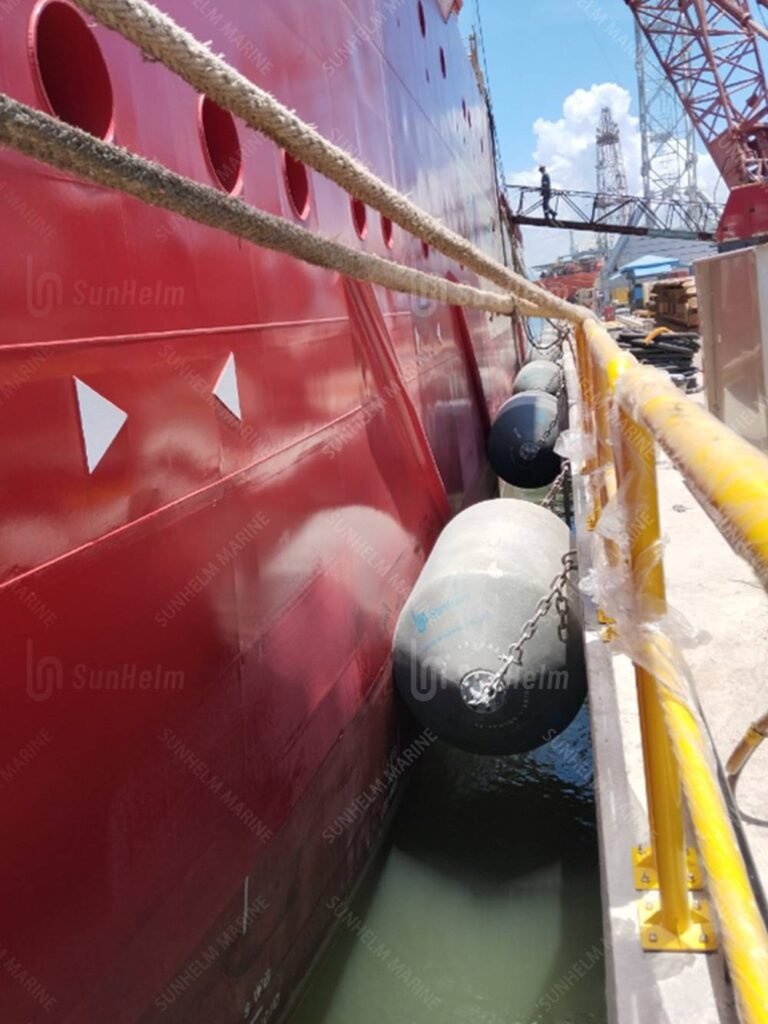
Performance Comparison
Energy Absorption and Reaction Force
- Foam fenders can absorb more energy per square meter, making them ideal for heavy-duty docking or high-impact areas.
- Pneumatic fenders deliver lower reaction forces, which means less stress on a vessel’s hull—great for sensitive or lightweight vessels.
Durability and Damage Response
- Foam fenders resist punctures and continue floating even if damaged.
- Pneumatic fenders, if punctured, may deflate and lose functionality entirely, requiring immediate attention.
Maintenance and Operational Cost
Maintenance Needs
- Foam fenders need minimal maintenance—just surface checks for cuts or wear.
- Pneumatic fenders require regular pressure checks and re-inflation at least once a year.
Transportation and Handling
- Pneumatic fenders can be deflated and stored compactly, which cuts down shipping and storage costs.
- Foam fenders are bulky and heavier, often increasing transportation and installation expenses.
Cost Consideration
- Foam fenders usually cost 2–3 times more than pneumatic fenders of the same size.
- However, in heavy-duty applications where durability and maintenance matter more than initial cost, foam fenders might be a better investment.
Application Scenarios
Use Case | Recommended Fender | Why |
---|---|---|
Offshore platforms, LNG terminals, ship-to-ship transfers | Pneumatic Fender | Flexibility, low hull pressure, ideal for varied tide conditions |
Cruise terminals, ferry docks, marina berths | Foam Fender | Low maintenance, tough exterior, no risk of deflation |
High wave or harsh environments | Foam Fender | More rugged, better resistance to damage and weather |
Temporary berths or military ports | Pneumatic Fender | High waves or harsh environments |
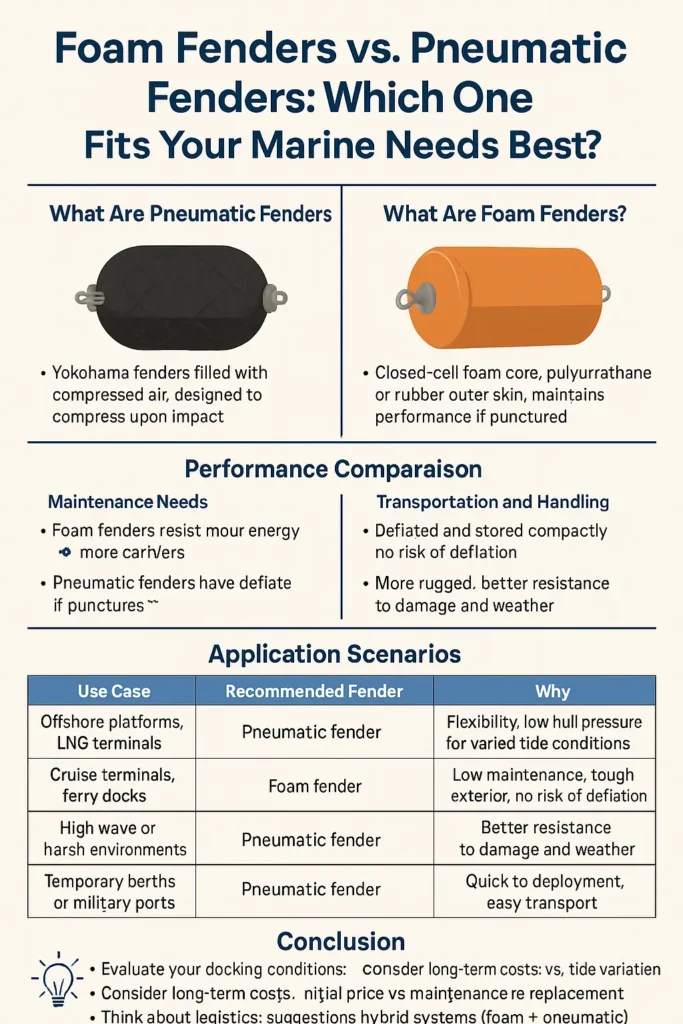
Choosing the Right Fender: What to Consider
To make the right decision:
- Evaluate your docking conditions: vessel type, wave exposure, tide variation.
- Consider long-term costs: initial price vs. maintenance and replacement.
- Think about logistics: will you need to move or store the fenders often?
- Consult experts: Sometimes hybrid systems (foam + pneumatic) offer the best results.
Conclusion
Foam and pneumatic fenders serve different purposes. Foam fenders offer resilience and reliability in harsh environments but come at a higher cost and logistical demand. Pneumatic fenders are cost-effective, flexible, and ideal for temporary or sensitive operations.
Need help choosing the best fender for your port or vessel? At Sunhelm, we provide expert consultation and a full range of marine fender solutions tailored to your needs.