The maritime industry is a bustling ecosystem, with vessels of all sizes constantly on the move. Among the many complex operations that take place at sea, Ship-to-Ship (STS) transfers are particularly critical. These involve two vessels mooring alongside each other to transfer cargo, often oil or gas, in open waters. While highly efficient, STS operations come with inherent risks. This is precisely where pneumatic fenders become not just helpful, but absolutely essential.
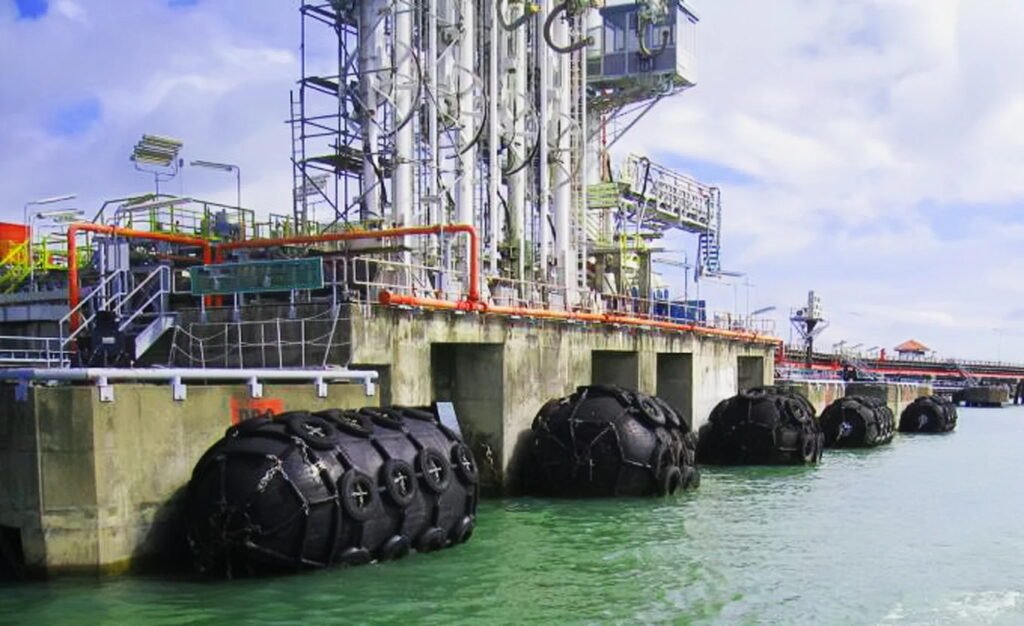
Imagine a massive oil tanker, weighing hundreds of thousands of tons, gently approaching another equally colossal vessel in the vastness of the ocean. Even with the most skilled crew and advanced navigation systems, the sheer inertia and movement of these giants mean contact, however slight, is inevitable. Without adequate protection, this contact could lead to catastrophic damage to hulls, spills of precious cargo, and even environmental disasters. This isn’t a hypothetical fear; incidents, though rare, can and do occur, underscoring the urgent need for robust safety measures. That’s why at Sunhelm, we emphasize the critical role of specialized marine fenders, and particularly pneumatic rubber fenders, in ensuring these operations are conducted safely and efficiently.
Pneumatic fenders, often referred to as ship fenders or marine fenders, act as vital shock absorbers between vessels during STS operations. They are essentially large, inflatable rubber cylinders filled with compressed air, designed to absorb the kinetic energy of impact and distribute the load evenly across the hull surfaces.
So, why are these seemingly simple devices so crucial? Let’s dive deeper into their indispensable role.
The Essential Role of Pneumatic Fendering
When two ships meet at sea for an STS operation, immense forces are involved. Even slight waves or currents can cause vessels to surge and sway, leading to potential collisions. Here, the unique properties of pneumatic fenders truly shine.
1. Superior Energy Absorption for Vessel Safety
Unlike rigid fendering systems, pneumatic fenders deform under pressure. This allows them to absorb a significant amount of kinetic energy from impact. This “cushioning” effect drastically reduces stress on a ship’s hull. It prevents dents, punctures, and structural damage. This is a primary reason we choose them for sensitive operations involving valuable cargo and delicate vessel structures.
2. Minimizing Hull Pressure with Flexible Design
The large contact area and flexible nature of pneumatic fenders ensure that impact force distributes over a wider area of the ship’s hull. This results in significantly lower hull pressure compared to solid fenders, further minimizing damage risk. For owners of various vessel types, from cargo ships to LNG carriers, this directly translates to reduced maintenance costs and extended vessel lifespan.
3. Adaptability for Diverse Hull Shapes
Ships’ hulls are rarely perfectly flat. Pneumatic fenders, with their inherent flexibility, conform to the contours of different hull shapes. They provide effective protection even on vessels with curves or protrusions. This adaptability makes them incredibly versatile for a wide range of ship-to-ship transfer scenarios.
4. Easy Deployment and Compact Storage
Compared to some other fendering solutions, pneumatic fenders are relatively lightweight when deflated. Crews can easily deploy and retrieve them. They also deflate for compact storage, optimizing deck space—a valuable commodity on any vessel.
5. Proven Reliability in Harsh Marine Environments
High-quality pneumatic rubber fenders are designed for the demanding marine environment. They withstand extreme temperatures, UV radiation, and abrasive forces. Their robust construction ensures long-term performance and reliability, even in challenging weather conditions. At Sunhelm, our marine fenders are engineered for durability and consistent performance, reflecting our commitment to safety and operational excellence.
If you’ve ever witnessed an STS operation, you’ll understand the delicate dance involved. The precision required is immense, and the margins for error are razor-thin. This is why investing in high-quality pneumatic rubber fenders is not just a safety measure, but a strategic decision for any company involved in maritime operations. They are the silent guardians, ensuring that vital cargo reaches its destination safely. They protect valuable assets and safeguard our precious marine environment. When it comes to Ship-to-Ship transfers, compromise on fendering is simply not an option.
FAQ:
What are pneumatic fenders used for?
Pneumatic fenders serve as protective barriers during ship-to-ship (STS) transfers, ship-to-dock berthing, and offshore operations. They absorb impact energy and prevent damage to vessel hulls.
How do pneumatic rubber fenders work?
Pneumatic rubber fenders work by utilizing compressed air inside a robust rubber outer layer. When a vessel makes contact, the air inside compresses. This absorbs the kinetic energy of the impact and distributes the force evenly over the hull surface, acting as a shock absorber.
What is the difference between pneumatic fenders and foam-filled fenders?
Pneumatic fenders are air-filled; they rely on air compression for energy absorption, offering high elasticity and low hull pressure. Foam-filled fenders, conversely, are filled with closed-cell foam. They absorb energy through the foam material’s compression and deformation, often providing good unsinkability even if punctured.
What are the advantages of using marine fenders in STS operations?
Using marine fenders, especially pneumatic rubber fenders, in STS operations offers several advantages. These include superior energy absorption, reduced hull pressure, adaptability to various vessel shapes, ease of deployment, and proven reliability in harsh marine conditions. All these contribute to safer and more efficient transfers.